Rail
The rail industry is under constant pressure to deliver safe, reliable, and efficient transportation — all while managing vast infrastructure networks, aging rolling stock, and complex regulatory demands. Operators need to strike a balance between optimizing asset life cycles, minimizing service disruptions, and meeting increasingly stringent safety and sustainability goals.
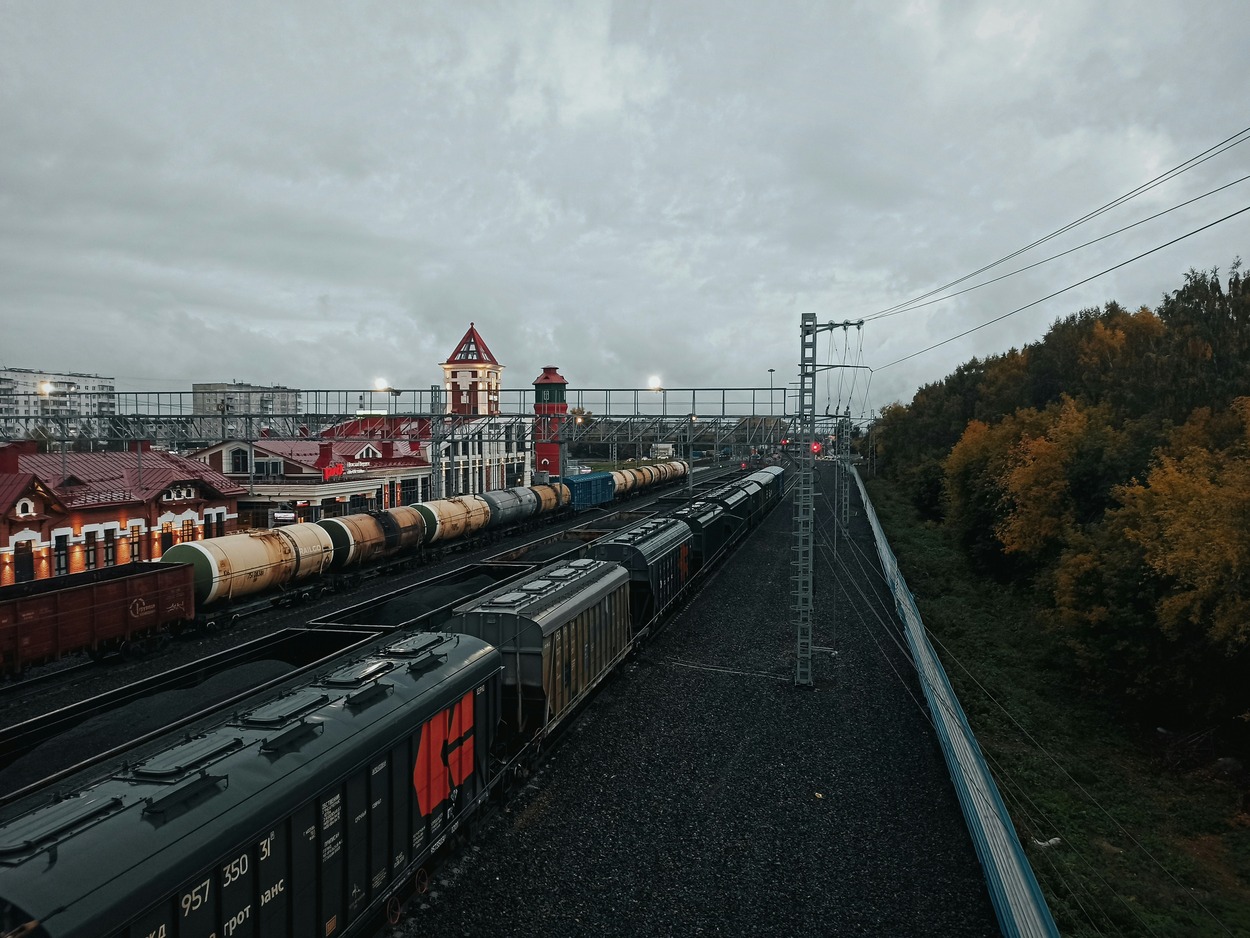
The IBM Maximo Application Suite (MAS) offers a comprehensive, intelligent solution that empowers rail organizations to proactively manage infrastructure, vehicles, safety compliance, and maintenance planning — all within one integrated platform. Whether it’s track, signals, stations, or rolling stock, MAS helps deliver smarter asset strategies, reduced lifecycle costs, and improved service outcomes.
Maximo Application Suite
Many networks are operating with aging tracks, vehicles, and signaling systems, leading to frequent breakdowns and safety concerns.
Asset Health Monitoring (Maximo Health)
Monitors asset conditions in real-time, flagging deterioration before failures occur.
Predictive Maintenance (Maximo Predict)
Uses AI/ML models and sensor data to forecast component failures on railcars, tracks, and switches.
Digital Twin Technology
Enables advanced simulations to understand wear and tear under real operational loads.
Unexpected failures can lead to train delays, commuter dissatisfaction, and regulatory penalties.
Condition-Based Maintenance
Automatically triggers alerts and work orders based on vibration, temperature, or usage thresholds.
Mobile Work Execution
Field teams can address issues quickly via mobile, improving response times and first-time fix rates.
Work Order Prioritization
Ensures critical issues affecting service continuity are addressed rapidly.
Rail operators must comply with strict safety, operational, and environmental regulations (e.g., FRA, OSHA, ISO standards).
Compliance Tracking & Inspection Scheduling
Automates regular inspections and maintains audit-ready records.
Permit-to-Work & Lockout/Tagout Procedures
Ensures safe execution of maintenance tasks in high-risk areas.
EHS Management (Environment, Health & Safety)
Captures incidents, risk assessments, and safety training certifications.
Rail assets such as tracks, overhead lines, and signaling systems are distributed across long distances, making visibility and maintenance planning difficult.
Linear Asset Management
Supports condition tracking and work planning for continuous assets like rail lines, power systems, and fences.
Geospatial Integration (GIS)
Provides map-based visualizations of track conditions, asset locations, and active work orders.
Inspection Data Integration
Streamlines input from track inspections, ultrasonic testing, and drone surveys.
Technicians, inspectors, and contractors work across stations, depots, yards, and trackside — often in remote or challenging environments.
Mobile Capabilities
Delivers work orders, instructions, and compliance checklists directly to devices, even offline
Crew Scheduling & Resource Optimization
Matches jobs with qualified staff and available equipment.
Time Tracking & Digital Sign-Offs
Increases accountability and reduces paperwork.
Planning for major renewals, replacements, and infrastructure upgrades requires deep insights into asset performance and costs.
Lifecycle Costing & Budgeting
Tracks total cost of ownership (TCO) and predicts when major investment is needed.
Capital Project Tracking
Supports infrastructure upgrades and major overhaul planning.
Data-Driven Decision Support
Uses historical data and predictive insights to justify capital expenditure.
Station facilities (HVAC, lighting, escalators, restrooms) directly impact passenger experience and service ratings.
Facility Maintenance Planning
Proactively manages the upkeep of all station amenities and mechanical systems.
Service Request Portals
Enables station staff or passengers to report issues and trigger responsive workflows.
SLA Tracking
Measures response times and issue resolution to meet service-level targets.
Rail operators face increasing pressure to reduce carbon emissions and energy consumption across trains, stations, and depots.
Energy Monitoring Dashboards
Tracks energy use of facilities and electric rail assets.
Sustainability Metrics & Reporting
Supports ESG initiatives by measuring water use, emissions, and carbon footprint.
Integration with Smart Building Systems
Enables automation for lighting, HVAC, and other energy-intensive systems.
Add value to your operations with Maximo Application Suite
Scalability
Supports growth and integration of new technologies like IoT and AI.
Centralized Operations
Unifies asset data, maintenance workflows, and performance monitoring.
Cost Savings
Reduces operational costs through optimized asset utilization and energy efficiency.
Strategic Decision-Making
Provides actionable insights to support investment and planning.
Explore how Maximo’s cutting-edge technology can revolutionize your approach to asset management, maintenance, and regulatory compliance.