Auto Manufacturing
Automotive manufacturers face intense pressure to maximize production uptime, maintain quality standards, and stay agile in an industry driven by innovation and global supply chains. As factories become smarter and more automated, managing thousands of assets — from robotic arms and conveyors to paint booths and assembly lines — becomes increasingly complex.
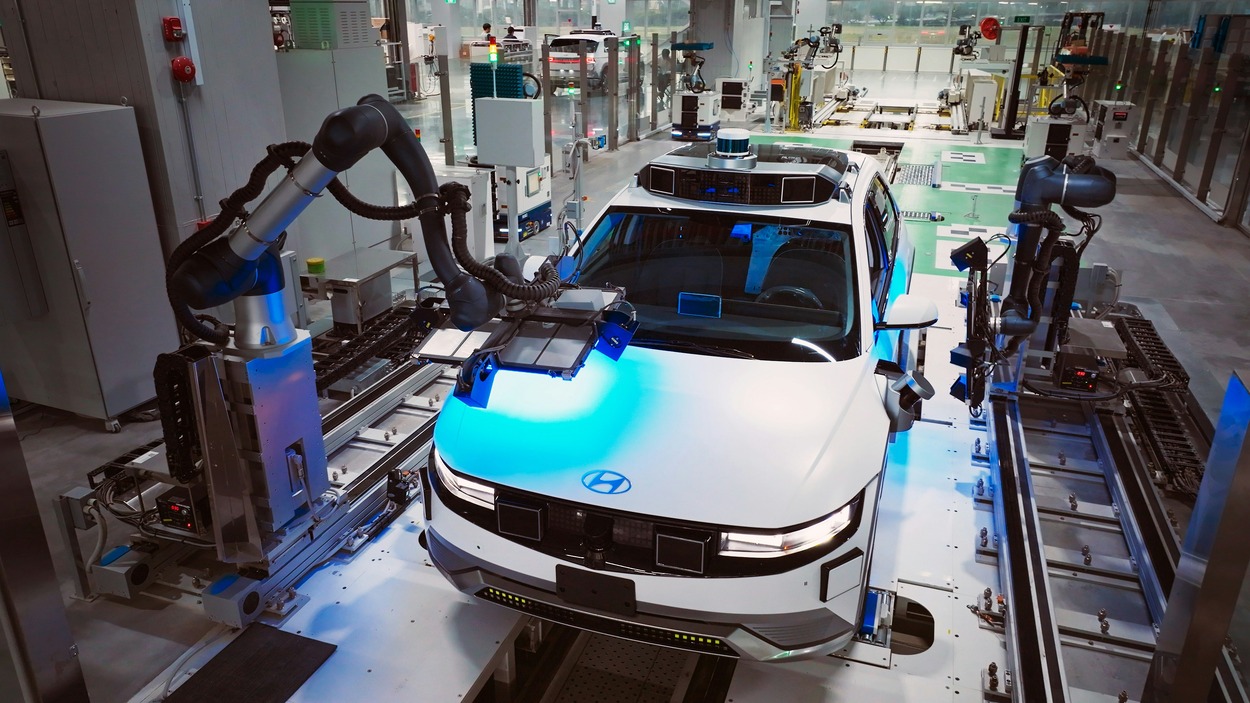
IBM’s Maximo Application Suite (MAS) delivers a unified, AI-driven platform that empowers auto manufacturers to optimize asset performance, predict failures, and streamline plant operations. With real-time insights, mobile access, and integration with modern factory systems, MAS supports world-class reliability and continuous improvement in fast-paced automotive environments.
Maximo Application Suite
Equipment failures on high-speed production lines lead to lost output, missed quotas, and production bottlenecks.
Predictive Maintenance (Maximo Predict)
Uses sensor data and AI models to forecast failures in robotics, conveyors, and presses.
Condition-Based Monitoring (Maximo Monitor)
Triggers alerts based on vibration, heat, or pressure changes to prevent breakdowns.
Work Order Prioritization
Ensures rapid response and resolution of line-critical failures to minimize disruption.
Managing thousands of diverse assets — from welding robots to chillers — across multiple lines and facilities is time-intensive and error-prone.
Centralized Asset Registry
Maintains a complete digital record of every asset, including service history, warranty, and location.
Multi-Site Configuration
Supports global plants while enabling local customization and standards.
Lifecycle Costing
Tracks performance and maintenance costs to inform replacement decisions and capital planning.
Faulty components or incomplete maintenance can affect product quality, triggering recalls or compliance violations.
SOP Enforcement in Workflows
Embeds standard procedures and quality checks into work orders.
Traceability Through Maintenance Records
Links equipment performance and maintenance to final product batches.
Deviations and Nonconformance Tracking
Captures issues and integrates with quality systems for investigation and resolution.
Highly automated plants rely on complex machines and robotics that require specialized maintenance and calibration.
Specialized Maintenance Scheduling
Handles preventive and condition-based tasks tailored for robotics and automation systems.
Skill-Based Assignment
Ensures technicians with the right training and certifications are assigned to advanced equipment.
Digital Twins & AI Insights
Simulates asset behavior to optimize usage and detect anomalies early.
Finding time to maintain equipment without disrupting throughput is a constant challenge on just-in-time (JIT) production lines.
Integrated Production & Maintenance Planning
Aligns maintenance windows with production cycles to reduce interference.
Work Scheduling Optimization
Matches available labor and parts with the least disruptive timing.
Downtime Analytics
Helps identify ideal maintenance windows and assess the true impact of repairs.
Assembly lines, paint booths, and automated guided vehicles (AGVs) all present safety hazards.
HSE Incident Management
Tracks safety inspections, incidents, and mitigation actions.
Permit-to-Work & Lockout/Tagout
Ensures work on hazardous equipment follows strict safety protocols.
Mobile Checklists & Safety Alerts
Guides technicians through safety procedures before work begins.
Auto manufacturers are under growing pressure to reduce energy usage, waste, and emissions across plants.
Energy Monitoring Dashboards
Tracks usage by area, asset, or line to identify overconsumption.
Green Maintenance Practices
Helps reduce water, chemical, and material usage through optimized workflows.
Sustainability KPIs
Measures and reports environmental metrics for compliance and corporate goals.
Many manufacturers are transitioning to Industry 4.0 but struggle to scale digital tools across legacy environments.
Cloud, On-Prem, and Hybrid Options
Offers flexible deployment for modern and legacy environments.
AI & IoT-Ready Architecture
Enables machine learning, edge computing, and IoT sensor integrations.
Mobile-Enabled Work Execution
Empowers frontline teams with smart tools, real-time data, and paperless workflows.
Add value to your operations with Maximo Application Suite
Scalability
Supports growth and integration of new technologies like IoT and AI.
Centralized Operations
Unifies asset data, maintenance workflows, and performance monitoring.
Cost Savings
Reduces operational costs through optimized asset utilization and energy efficiency.
Strategic Decision-Making
Provides actionable insights to support investment and planning.
Explore how Maximo’s cutting-edge technology can revolutionize your approach to asset management, maintenance, and regulatory compliance.