Enhancing Hydrant Inspections and Maintenance for Albuquerque Bernalillo County Water Utility Authority (ABCWUA)
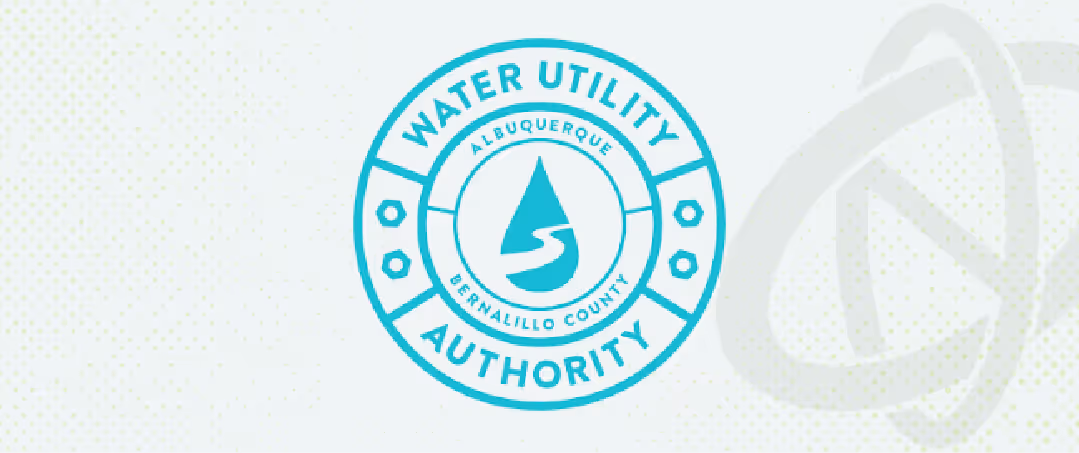
About
About ABCWUA
The Albuquerque Bernalillo County Water Utility Authority (ABCWUA) is the largest water utility in New Mexico, serving over 600,000 residents. With a vast network of water pipelines, sewer systems, and over $5 billion in assets, the authority is tasked with managing and maintaining critical infrastructure to ensure public safety. One of the essential aspects of their operations is fire hydrant inspections, which are required to be completed within a short, four-month window. ABCWUA needed an efficient, streamlined process to inspect over 14,000 hydrants annually.
To optimize the inspection and maintenance process, the utility turned to Naviam to integrate ArcGIS and IBM Maximo, ensuring a seamless, mobile-based inspection system that improves data accuracy and reduces manual processes.
Problem
Outdated Paper-Based Systems
ABCWUA faced several key challenges:
- Manual and Paper-Based Processes: Hydrant inspections were previously conducted using paper forms, which were inefficient and prone to errors. This was especially problematic given the large volume of hydrants to inspect within a limited timeframe.
- Lack of Integration Between Systems: The absence of integration between inspection data and the asset management system (Maximo) led to inefficiencies in creating work orders and tracking the status of hydrants.
- Ineffective Communication: Firefighters and the maintenance team needed a more efficient way to communicate inspection results and required follow-up work.
- Slow Process: Data entry was slow and prone to mistakes, reducing the overall efficiency of the hydrant maintenance process.
Solution
Integrating GIS with Maximo
Naviam provided an integrated solution using ArcGIS for mobile inspections and IBM Maximo for asset management. The solution involved:
- Mobile Inspections via ArcGIS Collector: Inspectors could now conduct hydrant inspections on mobile devices using ArcGIS Collector. The map-based interface enabled inspectors to easily select hydrants, fill out inspection forms, and access offline maps.
- Integration with Maximo: The solution used Naviam Workflows to automate the integration between ArcGIS and Maximo. Inspection data was automatically uploaded into Maximo, where relevant maintenance work orders were generated based on inspection results. This streamlined the entire process and ensured work orders were created and assigned promptly.
- Automated Work Order Creation: Workflows automatically created work orders in Maximo for repairs or maintenance actions based on the inspection data, and synchronized these results back to the mobile maps for field inspectors to track progress in real-time.
- Real-Time Data Visualization: Hydrants were symbolized on maps based on their inspection and maintenance status, allowing maintenance teams and fire crews to have immediate visibility of the hydrant system’s condition.
Result
Faster Response and Processing Times
The solution delivered significant benefits:
- Improved Efficiency: The mobile inspection solution drastically reduced manual data entry and errors, speeding up the process and enabling faster work order creation.
- Higher Data Quality: The use of ArcGIS reduced paper processing, leading to more accurate data collection and fewer mistakes.
- Better Visibility and Traceability: Maintenance teams could easily track the status of hydrants and work orders, improving accountability and visibility across the process.
- Accurate Work Prioritization: Maintenance work orders were prioritized based on real-time inspection data, ensuring that the most critical issues were addressed first.
- Rapid Deployment: With Naviam Workflows, the system was quickly deployed without the need for extensive development, allowing for swift implementation and updates to business processes.
- Manageability: The intuitive, no-code workflow logic made it easy for the business team to configure and manage the solution, significantly reducing the time and resources required for development.